Farrat offer a wide range of analysis, design and consultancy services, working on-site to find the right solution.
Consultancy
We provide an engineering led vibration and noise consultancy service for a broad range of clients across the manufacturing sector.
For more than 90 years combined, Farrat engineers have provided a worldwide on-site vibration consultancy and vibration analysis service to the manufacturers and users of all kinds of manufacturing and industrial machinery.
The primary objective of the service is to identify the causes of abnormal vibrations, especially those that degrade the quality of the finished product, whether this be in terms of its surface appearance or its accuracy and repeatability. All our vibration measurement and vibration analysis is carried out on-site using portable instrumentation and we are proud of our ability to respond rapidly to requests for assistance.
Our specialist range of consultancy services
Our expert team collaborates closely with manufacturers, OEMs, and buyers to identify, assess, and mitigate vibrations that can negatively impact productivity and the surrounding environment.
We are embarking on a new Knowledge Transfer Partnership project with the University of Salford. Part-funded by Innovate UK with the aim to create virtual prototypes to predict both noise and vibration of industrial equipment and building assemblies. The successful output would provide our customers with the ability to optimise isolation designs before installation.
To deliver a 360-degree full service post-construction monitoring surveys will validate the design performance. Allowing for the impact of external factors such as roads, railways or event venues located nearby.
We offer a comprehensive range of services, from procurement advice through commissioning, and even during refurbishment or decommissioning phases, ensuring that your equipment operates efficiently and with minimal disruption. With a commitment to environmental sustainability and decades of experience, we provide the peace of mind you need for smoother, more efficient operations
Other services
The stiffness of manufacturing machines, especially metal cutting machine tools such as machining centres, lathes and grinding machines, is important because it governs the magnitude of the displacement, or push-off, of the tool as it deflects under the influence of the cutting forces, and this of course affects the accuracy of the finished component.
In order to achieve the required component accuracy, a second pass comprising a lighter finishing cut has to be performed and this has a knock-on effect on cycle time. The accuracy of components produced by metal forming machines such as presses, guillotines, nibblers etc. can be equally undermined by lack of stiffness of the structure of the machine. Surface finish problems such as chatter marks associated with chatter vibration during cutting can also sometimes be attributed to a lack of stiffness of the machine on which the operation is being carried out.
An important part of investigating these problems is the measurement of the load-v-deflection characteristics of the machine so that problems of poor stiffness can be readily identified.
Our engineers, in some applications, go a step further and make use of modal analysis software to produce exaggerated, slow-motion animations of the way in which the structure distorts under load. This enables rapid identification of the exact source of the unwanted flexibility.
One of our greatest strengths lies in the experience we have gained over many years in the analysis of the resonant behaviour of structures.
Detailed modal analyses have been carried out on literally hundreds of structures of all types. Structures we have tested range from as small as a contact lens turning machine to as large as a steel rolling mill. This invaluable experience puts us in a unique position to be able to offer informed guidance in structural design, particularly in the design of new machinery of all types.
We can offer help at most stages in the design process, as shown in the adjacent idealised design process flowchart, but most particularly at the design review and prototype measurement and test stages.
Farrat specialises in delivering comprehensive Vibration Site Survey and Analysis Services, offering a crucial layer of protection for your valuable equipment. Our recommendation is to utilise these services proactively, ideally before the installation of your machinery, to mitigate the potential impact of low-frequency vibrations or shock inputs on the accuracy and throughput of your equipment.
It’s noteworthy that precision machine tool and measuring machine manufacturers establish specific allowable vibration specifications. This underscores the significance of thoroughly assessing and analysing vibration and shock criteria at the designated installation sites. Our dedicated engineering team conducts these vibration surveys globally, employing precise instrumentation to measure amplitude and frequency.
Ensuring the reliability of these measurements is paramount. Farrat accomplishes this through meticulous sensor calibration and equipment analysis solutions. This commitment to precision forms the foundation for delivering a thorough site vibration survey and analysis report. By consulting Farrat for these services, you’re essentially fortifying the long-term accuracy and reliability of your machinery.
In instances where vibration limits exceed the established thresholds, we provide personalised recommendations for isolation systems. To further your decision-making process, we also provide comprehensive before-and-after data for comparison. This holistic approach not only addresses current concerns but contributes to a proactive strategy for the sustained performance of your equipment.
Farrrat specialises in the intricate process of troubleshooting vibration problems across a diverse range of machinery, including but not limited to machine tools, drives, fans, motors, and pumps. The core objective in here is to conduct a thorough and precise diagnosis to pinpoint the underlying causes of vibrations.
A key focus of the troubleshooting process involves a meticulous examination to ascertain whether the vibration issue originates from defects within rotating equipment. This could encompass problems with bearings, gears, or issues related to imbalance in the machinery. Identifying these specific mechanical irregularities is crucial for devising targeted and effective solutions to rectify the problem at its source.
Furthermore, the diagnostic approach extends beyond merely identifying defects to encompass a nuanced understanding of resonant issues. It aims to determine whether the vibration problem is being amplified by resonant frequencies, even in cases where the vibration might seem normal under usual circumstances. This level of detail is pivotal in providing a comprehensive diagnosis and devising strategies to address not only the apparent symptoms but also the underlying factors contributing to the vibration challenges.
Our troubleshooting methodology has been refined since 1959 by delving deep into the intricacies of machinery dynamics. This comprehensive approach ensures that solutions are not generic but tailored to the specific causes of vibration problems, promoting sustainable and effective resolutions for enhanced operational performance.
We actively seek to take part in collaborative research both at UK and European levels.
Via their previous existence at AMTRI, our engineers benefit from a long association with a research and development environment and have been directly and indirectly involved in numerous research projects, including those funded by European programmes such as the Framework series and the earlier Brite and Esprit programmes. While at AMTRI, our engineers won funding via the DTI’s SMART programme to develop the post-process roll surface inspection system known as Chatter_Detect. Since its inception Chatter_Detect has now evolved to include in-process vibration monitoring during grinding helping operators find the best grinding conditions that minimise vibrations.
Recent Farrat industrial vibration control research projects include:
- KTP1 – in partnership with the University of Manchester and Innovate UK – 36-month R&D project exploring the detailed characterisation of Farrat’s isolation materials to drive improvements in manufacture and quality control and provide the ability to design new materials that are specifically designed for optimal performance in specific applications. Focus on supporting industrial applications but methods could be used for all applications.
- KTP2 – in partnership with Salford University and Innovate UK – 36-month R&D project exploring methods to predict behaviour and performance of isolated systems.
- IMPACT Project – 12-month R&D project to understand the performance of Farrat Industrial Vibration Control (IVC) solutions in-situ. Includes conducting a series of vibration measurement tests and analysis of key equipment installations using Farrat IVC solutions.
- AVM Performance Characterisation – 12-month R&D project testing and updating the performance of all Farrat Anti-Vibration Materials (AVM), covering load vs deflection, natural frequency and damping.
- HTZ Project – 12-month R&D project to analyse customer value-added processes in key industrial segments, with a view to drive product and service innovation.
Our engineering capabilities
Our engineering capabilities allow us to help you identify vibration sources and design the right vibration isolation solution for your application.
Our range of anti-vibration materials are manufactured in the UK and distributed worldwide across a wide range of industries. We are proud of the high performance these materials have provided our customers in their applications. Material properties such as stiffness, dynamic stiffness, damping, load bearing capacity, shape factor, creep and hysteresis are continually tested in our R&D facility to provide an assured performance.
We operate under an ISO 9001:2021 Quality Assurance System and under the international ISO 14001:2021 Environmental Management Standard.
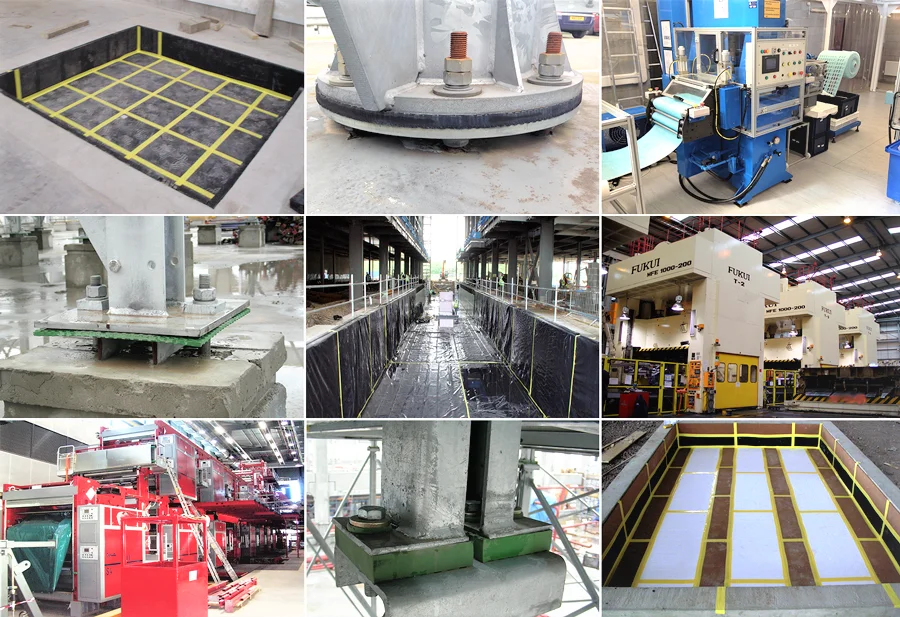
Latest case studies
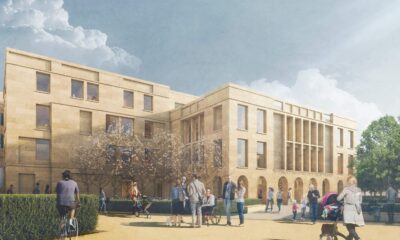
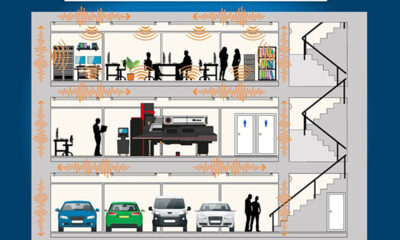
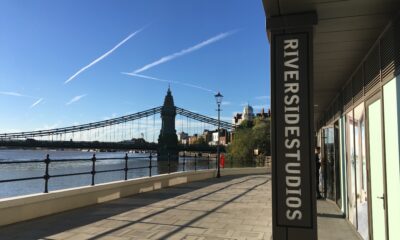
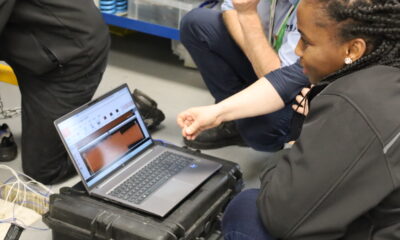
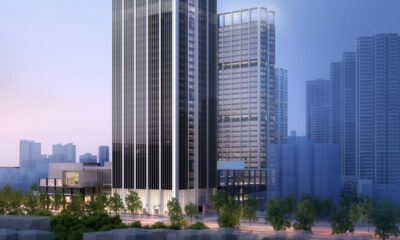
Challenge our engineers
Contact us now for an initial consultation.