The project involved demolition of an existing crescent building to construct a super-prime residential development opposite Regents Park in London. It is well summarised by the structural engineer, AKT here, the architect, PDP London, here and the acoustic consultant, Hilson Moran here. Demolition was carried out by McGee, the concrete frame was constructed by JRL Group who installed the bearings. Mid way through our contract Midgard took over as main contractor who carried out the high specification fit out.
Regents Crescent
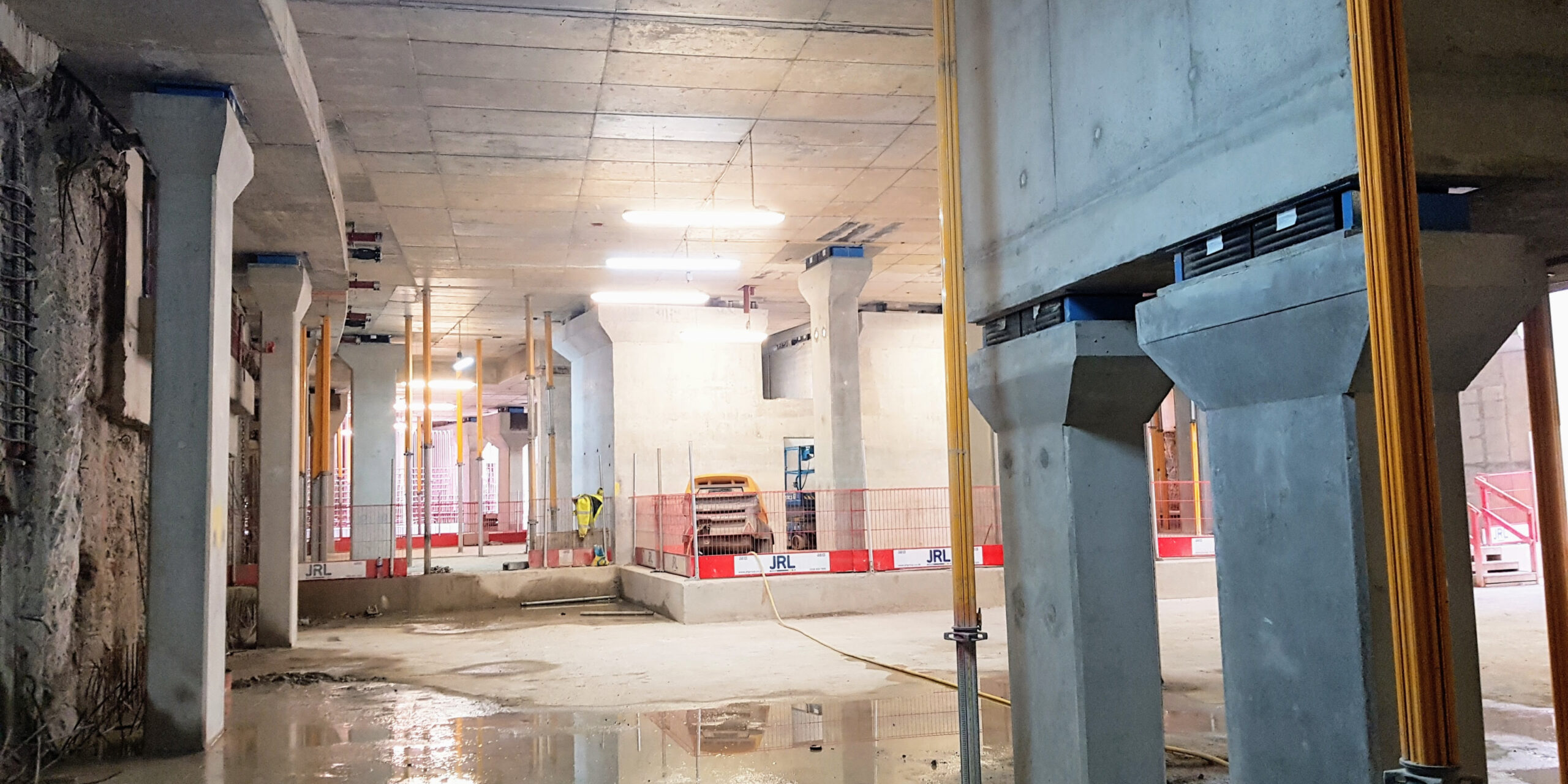
The Project
Key value we brought to the project
A highly complex project which Farrat worked through every detail to end up with a well-constructed acoustically isolated building. The whole system was manufactured by Farrat in the UK, delivered on time followed by significant installation support and inspection services all leading to a successful outcome.
Services, Products, System Supplied:
Perimeter Capping Beam
A capping beam is a structural element that ties all the perimeter retaining wall piling together. In Regents Crescent there were multiple scenarios and details around the site but the majority were based on the principle that the incoming soil pressure forces would pass through the ground floor slab and be cancelled out by the forces on the opposite side of the building.
Cores & Shear Walls
The cores accommodate lifts and staircases and together with shear walls provide all of the lateral restraint for the building. Since the cores were to be split under ground floor level this posed an additional challenge as the Farrat LNR Bearings used to support and acoustically isolate the structure are wider than the walls. LNR Bearings are manufactured with natural rubber which has a high bulk modulus meaning it maintains its density even when compressed resulting in bulging around the outside of the bearing. This means that larger bearings have relatively higher capacity than smaller bearings and therefore 1x large bearing (e.g. 500x500mm) will have significantly more vertical capacity than 4x 250x250mm bearings with the same build-up.
Columns
With such a large building there were a lot of columns. Since in most areas it was only a single level of basement the columns could be designed as key elements with effective length of x2. This simplified the acoustic design as it meant the column bearings only required fail-safes, no lateral restraints or vertical ties.
Acoustic Floating Floors
“With excellent project management and site supervision, delivered the project on time and on budget. Throughout the construction phase, I witnessed complete co-operation between Midgard, Farrat and our other sub-contractors. I can confidently recommend Farrat for works of this nature and look forward to working with them again.”
Retained Façade & adjoining buildings
Slip membrane for heritage façade
One feature that we supported the project with (as a favour) was to provide a slide bearing/ slip membrane to sit underneath the new heritage façade and prevent it from cracking either from movement in the foundations and thermal expansion and contraction of the façade itself. The vertical load was ~100 kN/m
Related Projects
Challenge our engineers
Contact us now for an initial consultation.