Contact us now for an initial consultation.
News
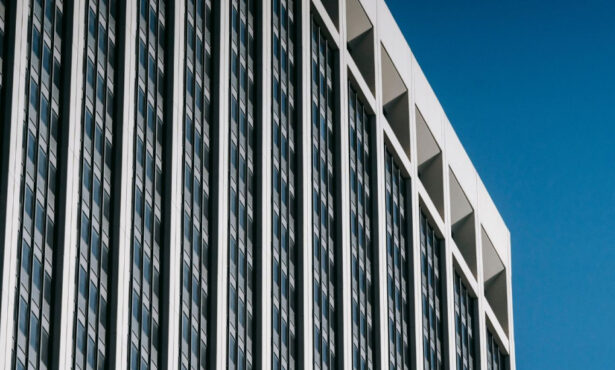
September 22, 2023
News 
September 12, 2023
News November 29, 2022
News September 29, 2022
News Contact us now for an initial consultation.